مراحل تولید فولاد
فولاد یکی از مواد مهم در ایجاد پایههای جامعه صنعتی است. که در صنایع مختلف اعم از ساخت و ساز، ساختمانسازی و ساخت انواع قطعات استفاده میگردد. این مادهی آهنی از مقادیر کمی کربن و عناصر آلیاژی طی مراحلی که به آن مراحل تولید فولاد گفته میشود، تشکیل یافته است. نیاز جهانی به تولید فولاد روز به روز، رو به افزایش بوده و دنیای مدرن را نمیتوان بدون این فلز ارزان و همه کاره، تصور نمود. اهمیت کاربرد فولاد در صنایع بر همه آشکار بوده و فولاد پس از سیمان دومین کالای تولید انبوه در جهان محسوب میشود. سابقه تولید فولاد در ایران به بیش از پنجاه سال میرسد. و بیش از 96 درصد فولاد جهان در 36 کشور مختلف تولید میگردد. چین به عنوان بزرگترین تولیدکننده و مصرف کننده فولاد جهان شناخته میشود. و پیرو آن دو کشور ژاپن و روسیه فعال در این حوزه هستند. این سه کشور با هم تقریبا 40 درصد فولاد جهان را تولید میکنند.
به فرآیند و مراحل تولید فولاد از سنگ آهن و یا قراضه، فولادسازی گفته میشود. در ساخت آن پس از حذف ناخالصیهایی از قبیل سیلیسیم، گوگرد، نیتروژن، فسفر و کربن اضافی (مهمترین ناخالصی) از آهن، عناصر آلیاژی مانند نیکل، وانادیوم، منگنز، کروم و کربن برای تولید گریدهای مختلف فولاد به آن اضافه میگردد.
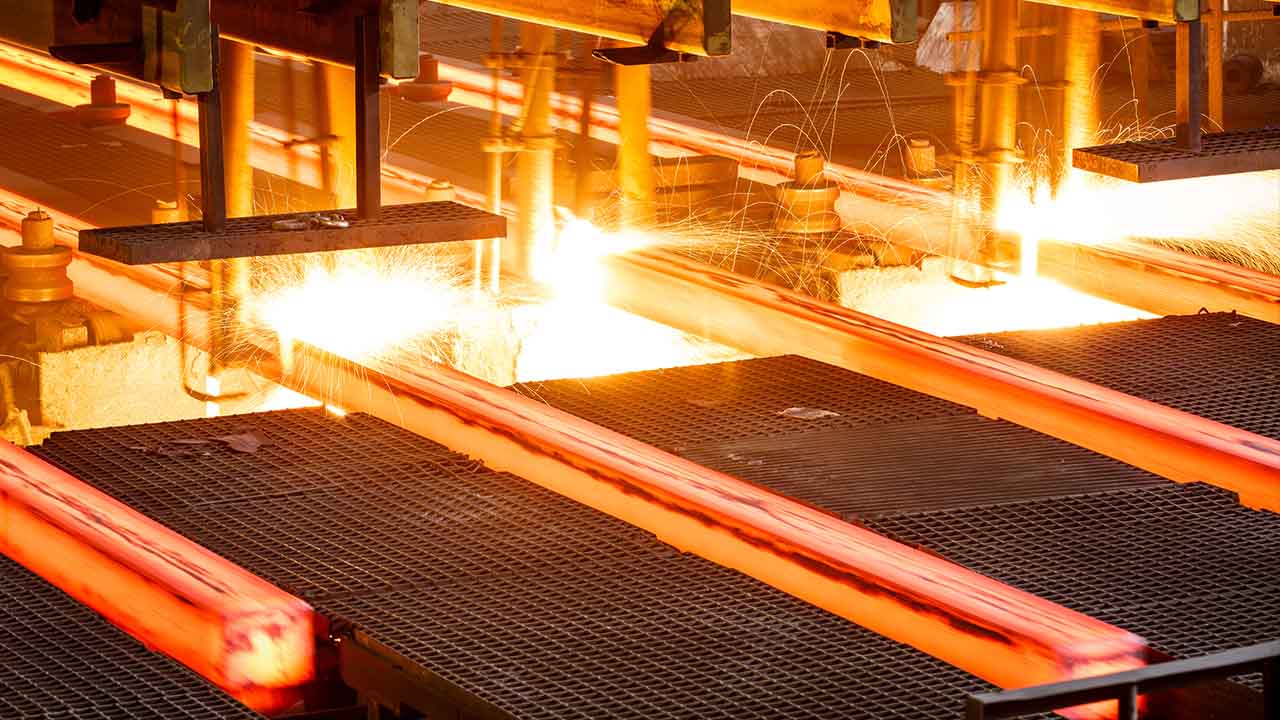
تاریخچه تولید فولاد در جهان
فولاد سازی از هزاران سال پیش وجود داشته است، اما تا اواخر قرن ۱۴ در مقیاس عظیم تجاری نشده بود. در دهههای ۱۸۵۰ و ۱۸۶۰، بسمر (Bessemer ) و زیمنس-مارتین (Siemens-Martin)، باعث تبدیل فولادسازی به یک صنعت سنگین شدند.
تولید فولاد در ایران
تولید فولاد در ایران به دو روش زیر انجام میشود.
1. در روش اول فولاد در کورههای احیای اکسیژن با مذاب آهن خام حاصل از کوره بلند و تهیه آهن خام یا چدن مذاب در کوره بلند صورت میگیرد. این روش بیشتر در ذوب آهن اصفهان استفاده میگردد. روش کار بدین صورت است که سنگ آهن به همراه آهک و کک وارد کوره بلند شده و آهن خام تولید میشود. در مرحله بعد این آهن خام به فولاد مذاب تبدیل شده و پس از جدا شدن ناخالصیها فولاد خام تولید میگردد.
2. در روش دوم نیز احیای مستقیم سنگ آهن و ذوب آهن قراضه و اسفنجی در کورههای الکتریکی از قبیل قوس الکتریکی و تولید انواع شمش فولادی، در فولاد خوزستان و مجتمع فولاد جنوب انجام میشود. فولاد سازی با کورههای قوس الکتریکی و القایی انجام میشود. به دلیل کمبود قراضه آهن در ایران در این روش بیشتر از آهن اسفنجی استفاده میگردد. درنتیجه درصد بالایی از فولاد خام توسط آهن اسفنجی تولید میشود.
مواد تشکیل دهندهی فولاد
فولاد آلیاژی از آهن و کربن است. آهن بهعنوان عنصر اصلی و کربن نیز مهمترین عنصر آلیاژی در تمام فولادها یافت میشوند. امکان دارد سایر عناصر در ترکیب شیمیایی فولادها وجود نداشته باشند، ولی عدم وجود کربن در فولاد ضروری بوده و نبود آن به معنای این است که این ماده فولاد نیست. مقدار کربن در ترکیب شیمیایی فولاد مهمترین بخش آن به شمار میرود. و بر همین اساس به انواع مختلفی تقسیم میشوند. لازم به ذکر است که فولاد و انواع آن قدرت، کاربردها و مزایاهای مختلفی دارند.
مهمترین عناصر ترکیب شیمیایی انواع فولاد
کربن
کروم
مولیبدن
وانادیم
سیلیسم
نیکل
منگنز
آلومینیوم
بور
تیتانیم
گوگرد
فسفر
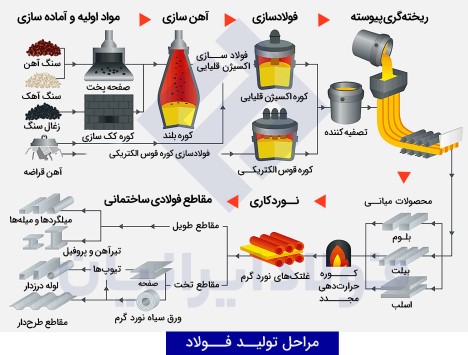
روشهای مختلف تولید فولاد
امروزه کاربرد فولاد بر کسی پوشیده نیست. زنجیره تولید فولاد، اصطلاحا به مراحلی گفته میشود که طی آن مواد اولیهی تولید فولاد به محصولاتی مانند شمش، ورق، نبشی، تیرآهن و...تبدیل میگردند.
برای تولید این محصول چهار روش مختلفی وجود دارد. ابتداییترین نوع این روش، روش کوره باز نام دارد که در طی زمان با روی کار آمدن روش بسمر، جایگاه خود را از دست داده است. به مرور با توسعهی روش بسمر زمان فولادسازی با کوره اکسیژن قلیایی به دیگر روشها افزوده شد.
هم اکنون تولید فولاد به روش BOF ( Basic Oxygen Furnace ) یا کوره اکسیژن قلیایی متداولترین این روشها بهشمار میرود. کوره قوس الکتریکی هم جدیدترین روش مراحل تولید فولاد در صنعت فولادسازی به شمار میرود.
به طورکلی زنجیره تولید فولاد شامل 4 مرحله است:
• معدن و استخراج سنگ آهن
استخراج سنگ آهن اولین مرحله در زنجیره تولید فولاد به شمار میرود. زیر بنای تولید محصولات فولادی سنگ آهن است. که پس از کشف معادن با استفاده از تجهیزات و ماشین آلات مختلف، این ماده استخراج میگردد.
• فرآوری
پس از استخراج سنگ آهن از معدن، مرحله فرآوری و تغلیظ شروع میشود. در این مرحله پس از انجام فرآیندهای مختلف، 2 نوع سنگ آهن بدست می آید:
سنگ آهن دانه بندی شده
کنستانتره آهن
• فولادسازی
در این مرحله کنسانتره بدست آمده در مرحله فرآوری، به مواد مذاب تبدیل و پس از انجام مواردی مثل خالص سازی، تزریق چندین نوع آلیاژ و گازهای مختلف، به فولاد خام تبدیل میگردد.
• نورد
آخرین مرحله از زنجیره تولید، واحد نورد است. در این مرحله فولاد بدست آمده در مرحله قبل را تغییر شکل میدهند. مرحله نورد ممکن است به شکل نورد گرم یا نورد سرد باشد.
روشهای متفاوتی برای نورد کردن استفاده میشود. از جملهی آنها میتوان به استفاده از غلتک برای شکلدهی ورق های فولادی و...اشاره نمود.
لازم به ذکر است که در این مرحله، محصولات نهایی مانند تیرآهن، ورق، شمش، نبشی و...به دست میآید. و شرکتهای مختلف و و بسیاری از تولیدکنندگان فولاد در ایران از این محصولات برای تولیدات خود استفاده میکنند. به عنوان مثال، ورق تولید شده نهایی در شرکت فولاد مبارکه در صنایع تولید لوازم خانگی، خودروسازی و....مورد استفاده قرار میگیرد.
روش ها و مراحل تولید فولاد
با توجه به تنوع موارد استفاده فولاد در دنیا تولید تغییرات بسیاری داشته است. در نتیجهی این تغییرات تولیدکنندگان سعی در استفاده از انرژی و سوختهای ارزانتر با توجه به محیط جغرافیایی خود و همچنین بالا بردن بهرهوری کردهاند.
امروزه فناوریهای مورد استفاده در تولید محصولات فولادی در مراحل بعد ریختهگری و نورد، تقریبا یکسان است. ولی برای به دست آوردن فولاد مذاب یا خام، از روشهای مختلفی استفاده میشود که شرح آن به صورت زیر میباشد:
1. تولید فولاد به روش کوره باز
کوره روباز یا باز ( Open hearth Furnace ) از قدیمیترین روشهای تولید به شمار میرود. و شامل یک کوره و سقفی حدودا کم عمق است. این کوره به نوعی طراحی شده که با ایجاد محیطی با حذف ناخالصیها از آهن خام، در فرآیند فولادسازی ، کمک میکند. با قرار گرفتن آهن خام در این کوره، ترکیب شعلههای باز و هوای گرم تولیدشده باعث تحریک و فعالیت شیمیایی و تولید فولاد میشود. حذف ناخالصیها و تولید فولاد درجات بالاتر و کاهش هزینههای تولید در فناوریهای جدید، باعث گردیده تا این روش به مرور زمان جایگاه خود را از دست بدهد.
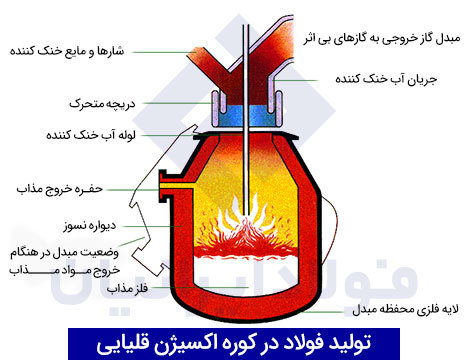
2. تولید فولاد به روش بسمر
این روش در سال 1856، توسط هنری بسمر (Bessemer) برای فرآیند تولید فولاد به روشی جدید به ثبت رسید. در این روش هوا از زیر کوره به آهن خامی که از کوره بلند بهدستآمده، دمیده شده و عمل احیای آهن انجام میشود. که این باعث سوختن کربن اضافی در فولاد خام، اکسید شدن ناخالصیها و رفتن آنها به سرباره میشود. همچنین اکسیداسیون باعث ایجاد و حفظ گرمای زیاد لازم برای فولادسازی میگردد.
در زمان استفاده از کورههای باز فقط یک بار در روز امکان بار ریزی وجود داشت. با ابداع روش بسمر فقط 12 دقیقه زمان برای تولید 5 تن فولاد لازم است.
لازم به ذکر است که فولاد تولیدشده به روش بسمر بسیار باکیفیت و مستحکمتر از فولاد تولید شده به روش کوره باز میباشد.
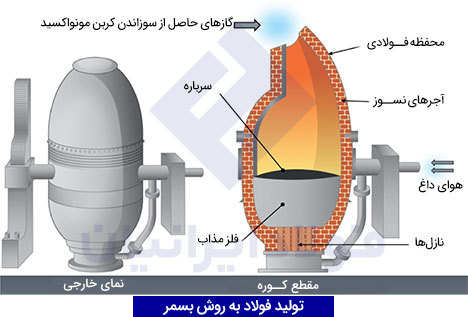
مطلب مرتبط: روشهای تولید فولاد
3. تولید فولاد به روش کوره الکتریکی
EAF یا روش کوره الکتریکی ( Electric Arc Furnace ) بعد از BOF، EAF بیشترین سهم را ( حدود 30% ) در تولید فولاد جهان دارا میباشد. ظرفیت تولید کوره الکتریکی حدود 25 تا 200 تن فولاد در هر بار مذابریزی است. زمان بین هر دو بار ریزی در این کوره حدود 4 ساعت بوده و زمان فرآیند ذوب در آن 2 ساعت طول میکشد. در این روش تولید، امکان تولید فولاد ابزار، آلیاژسازی و فولاد ضد زنگ وجود داشته و از مزایای آن به شمار میرود.
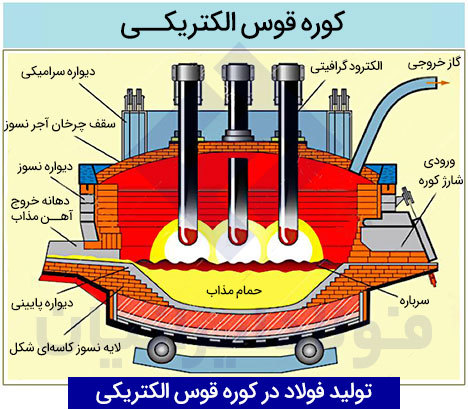
مشخصات فنی مهندسی مراحل تولید فولاد
جهت انجام مهندسی کامل یک کارخانه و مراحل تولید فولاد از بخشهای زیر استفاده میگردد:
• سازه
• پایپینگ و سیالات
• مکانیک
• ابزار دقیق
• فرآیند (عمومی و تکنولوژی)
• نسوز
• اتوماسیون
• سیویل
• برق
• معماری
تجهیزات اصلی در واحدهای صنعت فولاد
علاوه بر ضروری بودن داشتن اطلاعات در ارتباط با مراحل تولید فولاد، داشتن اطلاعات در زمینه، مهمترین تجهیزات اصلی واحدهای صنعت فولاد در هر کارخانه نیز ضروری است. این تجهیزات و واحدها به صورت زیر میباشد:
واحد نورد
واحد گندله سازی
واحد فولاد سازی
واحد کنسانتره
واحد احیاء مستقیم
مقاطع فولادی و مراحل تولید فولاد
تولید صنعتی در اواخر قرن نوزدهم آغاز و پیرو آن روشهای فولادسازی، به شکل قابل توجهی تکامل یافت. ولی با تمام این اوصاف روشهای مدرن همچنان بر اساس فرآیند بسمر ( روش استفاده از اکسیژن برای کاهش محتوای کربن در آهن ) اعمال میشود. همانطور که میدانید آهنسازی، اولین گام در ساخت فولاد میباشد. و با ذوب ورودیهای خام کک، آهک و سنگآهن در کوره بلند انجام میگیرد. آهن مذاب در این مرحله حدود 4 تا 4.5 درصد کربن و سایر ناخالصیها میباشد که باعث شکننده شدن آن میشود.
مرحله اول فولادسازی
مرحلهی اول فولادسازی، primary metallurgy نامیده میشود که تولید آن در کورههای BOF و EAF صورت میپذیرد.
مرحله دوم فولاد سازی
مرحلهی دوم از مراحل تولید فولاد فولادسازی ثانویه یا secondary metallurgy نام دارد. در این مرحله فولاد مذاب تولیدشده از هر دو مسیر BOS و EAF برای تنظیم ترکیب فولاد، تصفیه میشود. که با حذف یا اضافه کردن برخی عناصر خاص یا دستکاری اتمسفر یا دمای محیط تولید، صورت میگیرد.
شایان ذکر است که با توجه به انواع فولاد موردنیاز، قادر به استفاده از فرآیندهای فولادسازی ثانویه زیر میباشیم:
CAS-OB (تنظیم ترکیب شیمیایی با گاز آرگون یا اکسیژن)
Ladle furnace
Degassing
Stirring
Ladle injection
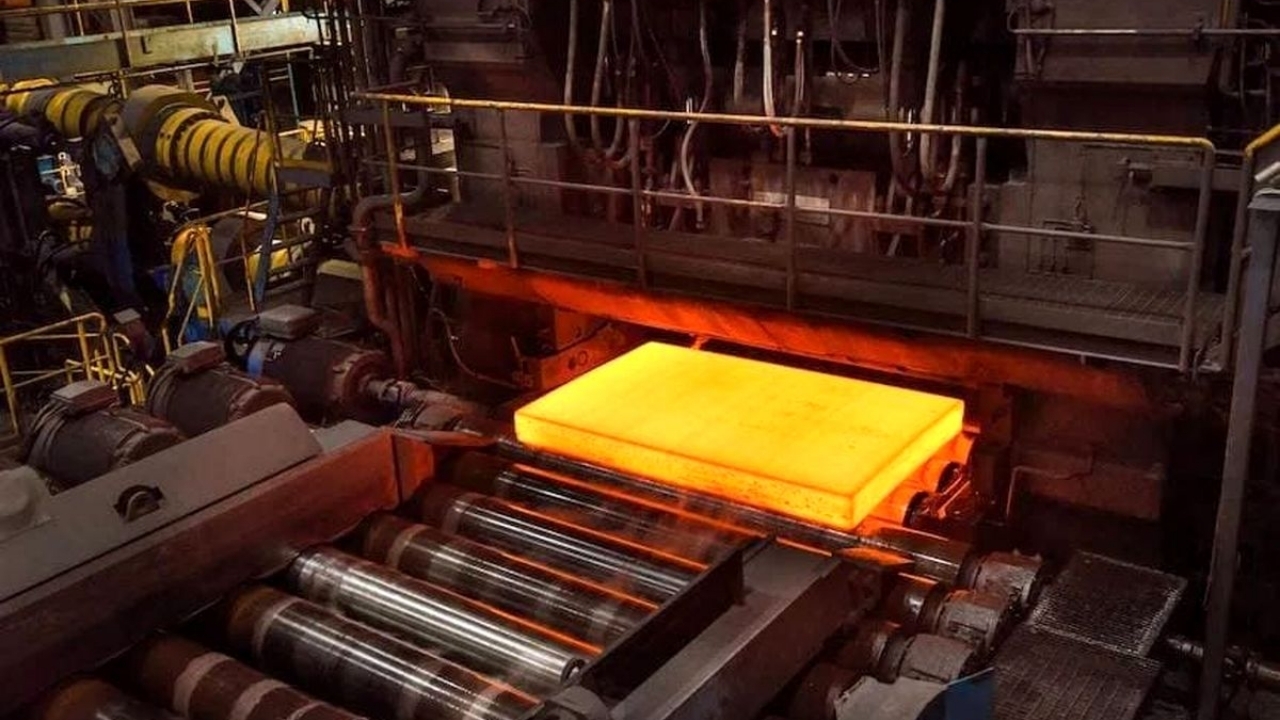
مطلب مرتبط: شمش بیلت و کاربردهای آن
مرحله سوم از مراحل تولید فولاد
زمانیکه به طور پیوسته و مداوم ریختهگری فولاد صورت گیرد، فولاد مذاب خنک شده در قالب باعث ایجاد یک پوسته فولادی نازک جامد میشود. مرحلهی بعدی شامل برش فولاد است که بسته به کاربرد، در شکلهای متنوعی برش داده میشود. این برشها شامل بلوم برای مقاطع (تیرها)، اسلب برای محصولات مسطح (صفحه و نوار) و بیلت برای محصولات بلند (سیم یا نوارهای نازک) میباشد.
فولادی که ریختهگری میشود در مرحله اولیهی شکلدهی، توسط نورد گرم به اشکال مختلف درمیآید. نورد گرم در واقع به فرایندی گفته میشود که باعث از بین رفتن عیوب ریختگی میگردد. و باعث میشود تا کیفیت و شکل قطعه به سطح مورد نظر برسد. محصولات بلند، لولههای بدون درز ، محصولات تخت و محصولات مخصوص جزو محصولات نورد گرم به شمار میروند.
مرحله نهایی تولید فولاد
و در آخر برای ایجاد خواص نهایی و شکل آن از تکنیکهای شکلدهی ثانویه استفاده میگردد. این تکنیکها عبارتند از :
ماشینکاری (حفاری)
عملیات حرارتی (تمپرینگ)
شکلدهی سرد (نورد سرد)
عملیات سطحی (کربندهی)
اتصال (جوشکاری)
پوشش دهی (گالوانیزه)
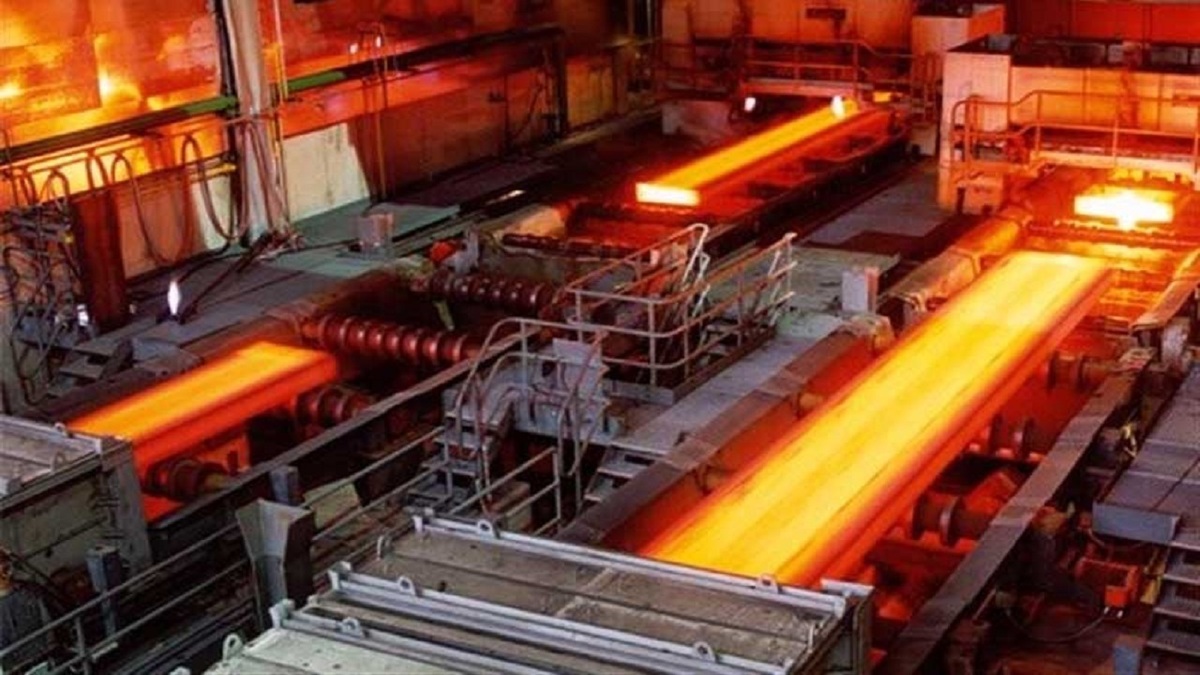
سخن نهایی
همانگونه که ذکر شد، به فرآیند استخراج سنگ آهن از معدن تا تولید محصول نهایی، مراحل تولید فولاد گفته میشود. این زنجیرهی تولید فولاد شامل 4 بخش معدن و استخراج سنگ آهن، فرآوری، فولادسازی و نورد است. کامل بودن این زنجیره، سودآوری بیشتری را به همراه داشته و باعث گردیده تا تولیدکنندگان با توجه به انواع استانداردهای فولاد ،
در پی تکمیل و بالا بردن سود تولیدات خود باشند.