نگاهی بر روی فولاد ضد زنگ: روشهای تولید و ترکیبات آن
همانطور که میدانید فولاد و انواع فولاد کاربردهای زیادی در زندگی دارد. همچنین در دهههای اخیر، فولاد ضد زنگ به عنوان یکی از جنبههای کلان صنعت مهندسی مواد به ویژه در حوزه مواد فلزی، توجه بسیاری از پژوهشگران و صنعتگران را به خود جلب کرده است. این فناوری پیشرفتهای چشمگیری را در زمینههای ترکیبات، روشهای تولید و کاربردهای مختلف فولاد ضد زنگ به ارمغان آورده است. در این سیاق، مقاله حاضر با عنوان "نگاهی عمیق بر روی فولاد ضد زنگ: ترکیبات، روشهای تولید و کاربردهای متنوع آن" به بررسی جزئیات فنی و تکنولوژیهای نوین این نوع فولاد میپردازد. این مقاله با هدف ارتقاء دانش علمی در زمینه فولاد ضد زنگ، از ترکیبات شیمیایی گرفته تا روشهای تولید پیشرفته و کاربردهای گسترده در صنایع مختلف، به بررسی گسترده و کاملی از این جنبهها میپردازد.
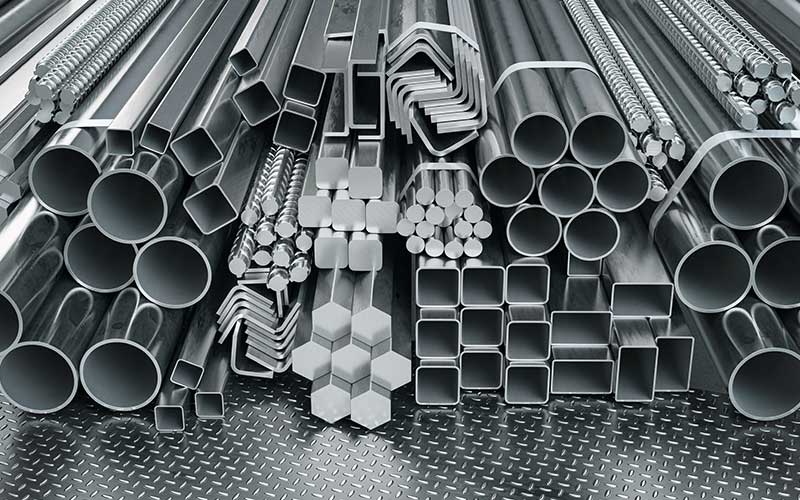
فولاد ضد زنگ چیست؟
فولاد ضد زنگ، یک نوع فولاد خاص است که با اضافه کردن عناصر آلیاژی به ترکیب آن از تأثیرات زنگ زدگی و زنگزدگی فلز جلوگیری میکند. این نوع فولاد اغلب شامل آهن (Fe)، کروم (Cr)، نیکل (Ni) و موارد دیگر مانند منگنز، مولیبدن یا تیتانیوم است. حضور کروم به عنوان یک عنصر اصلی در ترکیبات فولاد ضد زنگ باعث ایجاد پوششی نازک از اکسید کروم میشود که فلز را در مقابل اکسیداسیون و فرسایش حفاظت میکند. این خاصیت مقاومت به زنگ زدگی و خوردگی فولاد ضد زنگ آن را به یک انتخاب مناسب برای بسیاری از کاربردهای صنعتی، از جمله تولید وسایل آشپزخانه، ابزارهای پزشکی، تجهیزات دریایی، و صنایع خودروسازی تبدیل کرده است. به دلیل ویژگیهای مقاومتی و ظاهر زیبا، فولاد ضد زنگ همواره به عنوان یک ماده مورد توجه در تکنولوژی مواد معدنی و صنعت فلزات به شمار میرود.
مطلب مرتبط: فولاد ضد زنگ چیست و چه ویژگیهایی دارد؟
مراحل و روشهای تولید فولاد ضد زنگ
تولید فولاد ضد زنگ یک فرآیند پیچیده است که به کنترل دقیق ترکیبات شیمیایی، حرارت و سایر شرایط تولید نیاز دارد. مراحل اصلی تولید فولاد ضد زنگ عبارتند از:
1. انتخاب مواد اولیه
در ابتدا، مواد اولیه شامل آهن، کروم، نیکل و سایر عناصر آلیاژی به دقت انتخاب میشوند. این مواد باید به تعداد و نسبت مشخص باشند تا ویژگیهای خاص فولاد ضد زنگ به دست آید.
2. آمیختن مواد
مواد انتخاب شده در یک آسیاب مخصوص آمیخته میشوند تا ترکیب شیمیایی مطلوب حاصل شود. این مرحله از اهمیت بسیاری برخوردار است زیرا ترکیبات دقیق بر ایجاد ویژگیهای فیزیکی و شیمیایی فولاد تأثیرگذارند.
3. کورهگیری (Smelting)
مواد آمیخته شده به کورههای بلند خوراک داده میشوند. در این کورهها، تحت دماهای بسیار بالا، فرآیند کورهگیری آغاز میشود و تبدیل مواد به فولاد رخ میدهد.
4. تفالهزنی (Casting)
پس از کورهگیری، فولاد به صورت مایع به کمک تفالهزنی در قالبهای مختلف شکل گرفته و به صورت میلهها یا شاخههای فولادی اندازهگیری میشود.
5. آبکاری (Annealing)
آبکاری یک مرحله مهم است که در آن به فولاد به میزان مشخصی گرما داده میشود تا انجام فرآیند تقسیم دوبارهای و حذف تنشهای داخلی از فولاد امکانپذیر شود.
6. تغلیظ نهایی (Final Annealing) و پردازشهای پسازترمیم (Post-Heat Treatment Processing)
در مرحله نهایی، فولاد در دماها و شرایط خاصی تحت مراحل تغلیظ نهایی قرار میگیرد تا ویژگیهای نهایی و مطلوب به دست آید. پردازشهای پسازترمیم نیز جهت بهبود خصوصیات مکانیکی و شیمیایی فولاد استفاده میشوند.
7. برش و شکلدهی
در مرحله نهایی تولید فولاد ضد زنگ ،فولاد حاصل از مراحل قبلی به شکلدهی نهایی میپردازد. این شامل برش، تراشکاری و سایر عملیات فرآیندی برای تولید قطعات یا محصولات نهایی میشود.
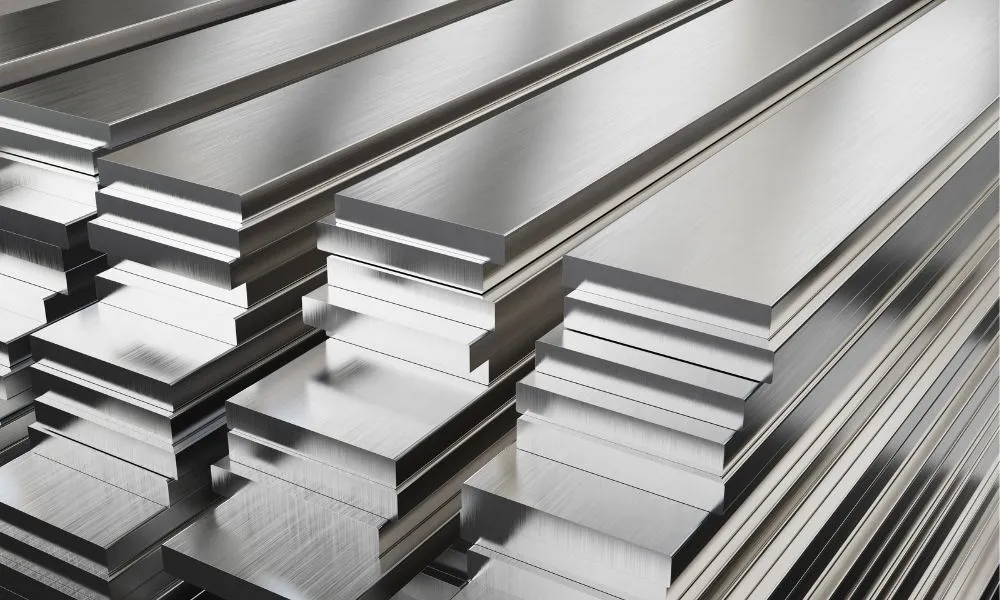
ترکیبات فولاد ضد زنگ
ترکیبات و ویژگیهای فولاد ضد زنگ متنوع هستند کاربرد مورد نظر، ترکیبات مختلفی از عناصر آلیاژی در آنها میتواند وجود داشته باشد. با این حال، ترکیبات اصلی معمولاً شامل آهن (Fe)، کروم (Cr)، نیکل (Ni) و موارد دیگر هستند. در ادامه به ترکیبات اصلی برخی از انواع فولاد ضد زنگ اشاره خواهیم کرد:
1. آستنیتی (Austenitic Stainless Steel)
- کروم (Cr): حدود 16 تا 26 درصد
- نیکل (Ni): حدود 6 تا 22 درصد
- منگنز (Mn): حدود 2 درصد
- کبالت (Co): حدود 1 درصد
- مولیبدن (Mo): حدود 2 تا 3 درصد
2. مارتنزیتی (Martensitic Stainless Steel)
- کروم (Cr): حدود 12 تا 18 درصد
- نیکل (Ni): حدود 1.5 درصد
- کبالت (Co): حدود 1 درصد
- کربن (C): حدود 0.1 تا 1.2 درصد
3. فریتیتی (Ferritic Stainless Steel)
- کروم (Cr): حدود 10.5 تا 30 درصد
- نیکل (Ni): حدود 0.1 تا 0.6 درصد
- منگنز (Mn): حدود 1.5 درصد
- آلومینیوم (Al): حدود 0.1 تا 0.3 درصد
4. پرسیپیتیتی (Precipitation Hardening Stainless Steel)
- کروم (Cr): حدود 14 تا 17 درصد
- نیکل (Ni): حدود 3.5 تا 5.5 درصد
- مس (Cu): حدود 3 تا 5 درصد
- تیتانیوم (Ti): حدود 1.7 تا 2.5 درصد
این ترکیبات تنها نمونهای از انواع فولاد ضد زنگ هستند و ممکن است در تولید فلزات با خصوصیات خاص، ترکیبات دیگری نیز بهکار گرفته شود. همچنین، اضافه کردن عناصر دیگر مانند سیلیسیم (Si)، فسفر (P)، سولفور (S) و افزودنیهای دیگر نیز میتواند به تغییر در خصوصیات فیزیکی و شیمیایی فولاد ضد زنگ منجر شود.
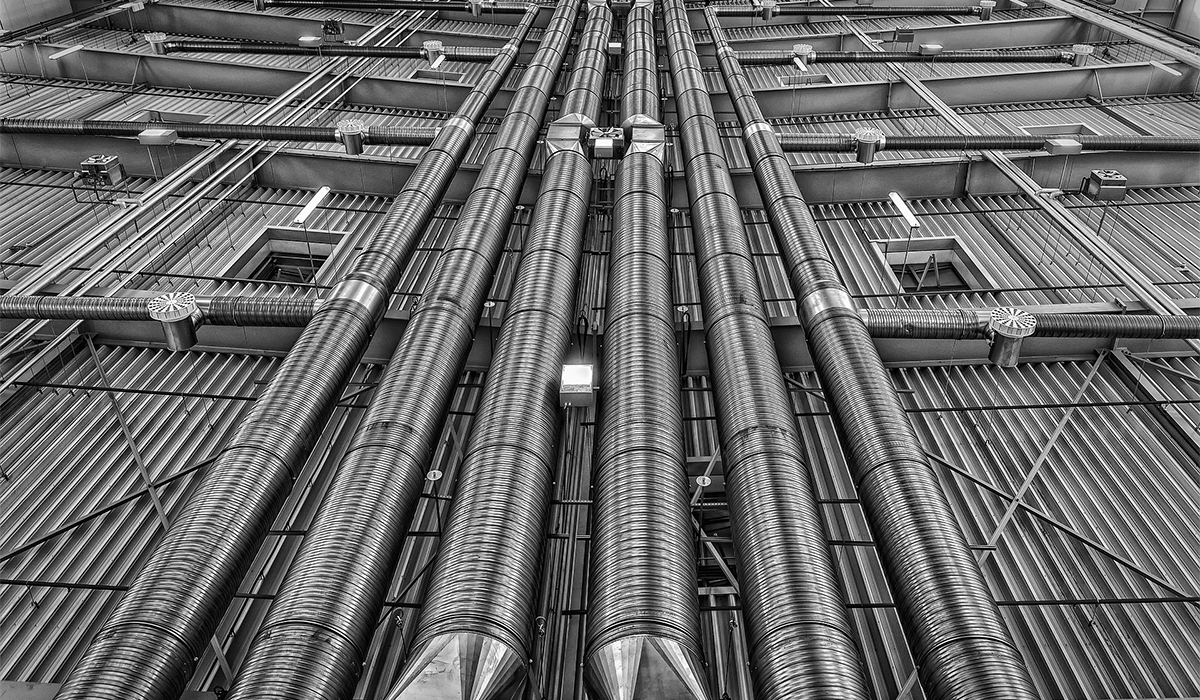
بهتر است بخوانید: کاربرد فولاد در صنایع
سخن نهایی
همانطور که گفته شد در دهههای اخیر، فولاد ضد زنگ به عنوان یکی از جنبههای کلان صنعت مهندسی مواد به ویژه در حوزه مواد فلزی، توجه بسیاری از پژوهشگران و صنعتگران را به خود جلب کرده است. همچنین به این مورد نیز اشاره شد که یک نوع فولاد خاص است که با اضافه کردن عناصر آلیاژی به ترکیب آن از تأثیرات زنگزدگی فلز جلوگیری میکند. در اصل تولید فولاد ضد زنگ با مراحب و ترکیبات مشخص شده نقش مهمی در صنعت فولاد سازی ایفا میکند و نیاز به کنترل دقیق فرآیندها و شرایط تولید دارند تا ویژگیهای مطلوب در فولاد حاصل شود.